- 会員限定
- 2018/01/30 掲載
なぜ今「鋳物」か? ロボット時代に向けたヤマハ発動機の「深慮遠謀」
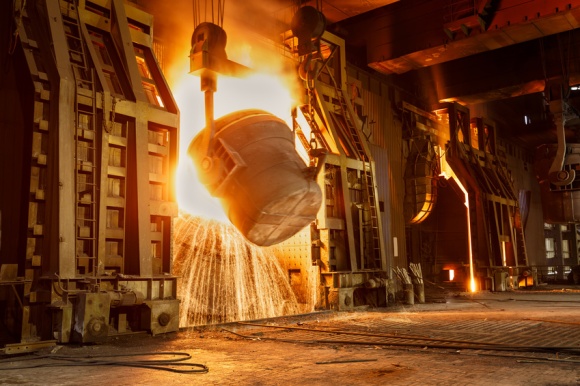
日本は自動車用を中心に世界第4位の「鋳物」生産国
日本でも「鋳物」は仏像から鍋、釜に至るまで身近な存在で、世界に知られる伝統工芸品の「南部鉄瓶」も「高岡銅器」も、鋳物の技術でつくられている。
イメージは地味だが、現代の産業も社会も金属鋳造の技術なくしては成り立たない。文房具や電子部品のような小物から建材、ロボット、自動車、航空機、宇宙ステーションまで、どこかで必ず利用されている。
鋳造技術でつくる「鋳物」の最大の用途は「自動車用」で、群を抜いている。経済産業省の「鉄鋼・非鉄金属・金属製品統計」によると、2016年の国内の銑鉄鋳物の生産量は323.4万トンだったが、その約64%の209.2万トンは「自動車用」で占められた。2位の「産業機械器具用」の約13%を大きく引き離している。
高度な鋳造技術が必要な「精密鋳造品」に限っても、2016年の5441トンのうち「自動車用」は3888トンで約72%を占める。
製品別シェアの6~7割が自動車用で占められるということは、「鋳物の技術なくして自動車はつくれない」とも「自動車産業は金属鋳造業にとっての生命線」とも言える。ちなみに銑鉄鋳物生産量が最多の都道府県は自動車産業の中心地の愛知県で、全国の37.4%を占める(2017年1~10月合計)。
だが、日本自動車工業会の統計によると2016年の自動車(四輪)の国内生産台数は920万台で、2007年の1159万台から20.6%減少。直近ピークの2012年の994万台と比べても7.4%減少した。その影響もあり鋳物の国内生産は頭打ちで、2012年と2016年を比較すると銑鉄鋳物全体では9.8%減で、自動車用は8.8%減少している。精密鋳造品もピークの2014年から2年で18.3%も減った。
ただし昨年2017年の上半期は、銑鉄鋳物の生産量は前年同期比4.9%増、精密鋳造品の生産量は3.0%増と、回復をみせている。
自動車の低燃費化につながる「軽量化」のニーズに応えるアルミニウム合金鋳物は、42万トン台で安定している。
2017年上半期の生産量は前年同期比3.7%増と上向きだった。アルミニウムはマグネシウムとともに将来性ある鋳造素材で、日本は非鉄金属を加工する鋳造技術では、中国やインドなど新興国に対して優位に立つ。
鋳物生産量の2015年の国別シェアは、43.8%の中国が突出した首位で、2位が10.3%のインド、3位が9.9%のアメリカで、日本は5位のドイツ(5.1%)をわずかにかわし、5.2%で4位というポジションにある(「Modern Casting」調べ)。
1位の中国、2位のインドは銑鉄鋳物が主で、製品の付加価値は必ずしも高くない。高度な技術力を要する精密鋳造品、アルミニウムやマグネシウムの鋳物、密閉中空鋳物、極薄肉鋳物のような高付加価値型の鋳造製品では、日本は3位のアメリカや5位のドイツと肩を並べ、世界をリードできる技術力、生産力を保持している。その用途は電気自動車(EV)やロボット、スマートフォンなど、21世紀後半に向けて有望な分野が並んでいる。
ヤマハ発動機は2017年、鋳物の委託生産に本格進出
2017年、二輪車、エンジン、小型ボート、船外機などを製造するヤマハ発動機が、鋳造製品の委託生産事業を本格展開すると報じられた。同社の「鋳物」製造の歴史は古く、ルーツ企業の日本楽器製造(現・ヤマハ)が1900年(明治33年)から生産するピアノの金属部品「フレーム」にさかのぼる。1955年(昭和30年)に日本楽器製造から分離・独立したヤマハ発動機は「自主開発・自主生産」がモットーで、二輪車の車体用部品で、エンジンで、船外機で、金属鋳造の独自開発技術を磨き、ノウハウを蓄積してきた。
その鋳造技術を活かし、外部の企業から積極的に受注する新事業を立ち上げた。本拠地は静岡県磐田市の「磐田製造部」で、ヤマハ発動機本体、関連会社の浜北工業と、2017年1月に東洋ベスク、ファインキャテックの両社が合併し誕生した100%子会社、ヤマハモーター精密部品製造が受注を受け持つ。
生産はインドネシア、タイ、ベトナム、インド、台湾、中国、ブラジル、日本という8つの国と地域でグローバルに展開。世界トータルで製造装置347台、生産能力はアルミ部品月産11600トン、鋳鉄部品月産1370トンという陣容(2017年5月現在)で、部品製造会社があるインドネシア、タイ、ベトナムの3ヵ国が生産の中心となっている。
生産規模でもわかるようにアルミニウム鋳造、それも二輪車の車体フレームで多用されてきた「アルミダイカスト」が大きな柱で、大型部品を薄肉で鋳造できる「CFダイカスト」という独自技術を持つ。それを応用し、アルミシリコン合金を使う世界初の「ダイアジル(DiASil)シリンダー」の開発に成功した。
海水にさらされる船外機の鋳造部品に採用した「アルミ耐食合金」は、海水中で使用されるモーターや潮風を受ける洋上風力発電機にも適した素材で、マリン事業で長年の実績があるヤマハならではの技術だ。タイヤホイール、シートフレームなどで使われる「マグネシウムダイカスト」も、マグネシウムは加工が難しい素材で、その技術で世界の最先端をゆく。
鋳造法では「LP(低圧)鋳造」や「GD(重力)鋳造」の技術があり、LP鋳造による中空鋳物は電気自動車(EV)用の水冷ジャケット付きモーターフレーム、LP鋳造、GD鋳造による結晶組織が緻密な鋳物はディーゼルエンジン用のシリンダーヘッドというように、有望な用途を開拓している。このようにヤマハ発動機は「鋳造のエキスパート」を自任するにふさわしい技術ラインナップを有している。
現在、引きあいを見込む需要先も、二輪、四輪の自動車や船舶以外では、軽量アームなどの産業用ロボット用部品、風力発電用部品、スマホ・携帯電話やその基地局用の部品、シートフレームなどの航空機用部品、鉄道車両用部品などに広がる。建築外装材、エクステリアも開拓したい分野といい、グローバルな受注拡大で、2年後の2020年までに外販受注年間100億円の達成を目標としているという。
【次ページ】自動車「軽量化」のニーズは生産されるクルマの数だけある
関連コンテンツ
関連コンテンツ
PR
PR
PR