- 会員限定
- 2019/01/09 掲載
デジタルツインとは何か? 最新事例から読み解く、取り組むメリット
フロスト&サリバン連載~産業別に見るICTのインパクト~
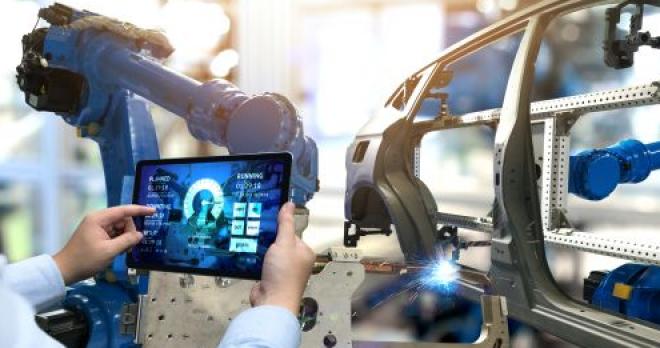
「デジタルツイン」とは? シミュレーションと何が違う?
生成されたデータはクラウド上で保存され、実際のビジネスにインパクトを及ぼす分析、次のアクションの提示などに需要が増大している。特に注目を集めているのが、今回取り上げる「デジタルツイン」である。
フロスト&サリバンでは、デジタルツインを以下のように定義している。
製品、製造機器、およびオペレーションに関するデータを蓄積および解析するソフトウェアソリューション。これらの情報が蓄積されており、簡単にアクセスすることができる。デジタルツインにより、企業は各製造段階で各機器や製品の状態をリアルタイムで確認し、適切な状態に保つことができる
より分かりやすく表現すると、デジタルツインは「サイバー空間上に実際の製品や製造工程を再現したシステム」と言える。静的なシミュレーションにとどまらず、各工程がリアルタイムに連携され、もう一つの現実をコンピュータ上に作り出すのである。
一般的なシミュレーションシステムとデジタルツインの違いは、「リアルタイム」および「現実世界との連動」という点である。
シミュレーションシステムは、理想的な設計仕様に基づいて複数のシナリオをテストすることができる。しかし、製造段階や工場から出荷された後に実際に使用され、摩耗が生じたケースまで考慮に入れることは難しい。
一方、デジタルツインでは、設計段階の製品のみならず、製造段階や出荷後についてもデータの収集と解析ができる。そのため、予防的保全やメンテナンス頻度についてより正確性を担保できる。
デジタルツインのメリット:予防保全
デジタルツインは、製造やサプライチェーンにおける各工程について効果を発揮する。製品設計の工程でデジタルツインを導入することで、過去の製品の製造工程や出荷後の不具合や、負荷がかかりやすい箇所についてのデータをすぐに入手することができる。「設計自体に問題があったのか、それとも使用している原料に問題があったのか、想定していないような使い方があったのか」など、かなりの精度で理解することができる。
今までは、製造部や営業部、顧客からの限られたフィードバックをベースに問題を特定し、そこから設計と検証を繰り返すことが必要だった。デジタルツインを活用することで、設計工程の生産性が高まることが期待される。また、デジタルツインを用いて設計した場合、試作の数を減らせるというコスト削減効果もある。
製品設計を綿密に行っても、製造工程でエラーが起きることは珍しくはない。組み立てラインに何らかの不具合が生じたのかもしれないし、パーツに不良品が含まれていた可能性もある。また、製造工程で使われる機器の消耗が進み、想定通りに動かないというケースもある。従来であれば、製造工程におけるエラーについては、熟練の作業員が時間をかけて原因を特定する必要があった。
一方、製造ラインにセンサーが取り付けられ、デジタルツインに連携されていれば、問題が発生した際の切り分けを迅速に行うことができる。また、デジタルツインにおいて製造工程のデータをリアルタイムで収集・分析することで「どこでエラーが起こる可能性が高い」かを事前に明示でき、予防的保全を実施することも可能になる。
デジタルツインのメリット:アフターサービスの充実
デジタルツインは、出荷後のアフターサービスにおいても効力を発揮する。顧客のもとに製品が出荷された後でも、デジタルツインにはその使用データが連携され続けている。その使用データを用いて、企業は各製品の摩耗状況を詳細に理解することができる。今までは、あるカテゴリにおいて区分けされた製品ごとに一斉メンテナンスを実施する必要があった。製品の使用度合いや環境によって消耗のレベルは違う。そのため、「同じカテゴリの製品でも一部は消耗の度合いが激しくメンテナンスの必要があるものの、その他の製品は実際にはメンテナンスが不要である」という状況は珍しくなかった。
消耗がさらに激しい製品の場合は、一斉メンテナンスを待たずに機能停止することもある。その場合はサプライヤー側が緊急メンテナンスをする必要があり、さらに悪いケースではその停止やエラーが原因で生じた被害に対して補償を実施することもあった。
デジタルツインを活用することで、上記のようなサービスプロセスの効率性は一気に向上する。連携されてきたデータを収集・分析し、故障が起こりそうな製品のみメンテナンスおよびパーツの交換を実施し、不要なメンテナンスコストをかける必要がなくなるからだ。その結果、製品の不具合による顧客への損害も最小限に食い止めることができる。
【次ページ】デジタルツインの事例:カナダ Veerum
関連コンテンツ
PR
PR
PR