- 会員限定
- 2019/06/04 掲載
製造業に「遺伝的アルゴリズム」はなぜ必要?メリットは?活用事例を交えて解説
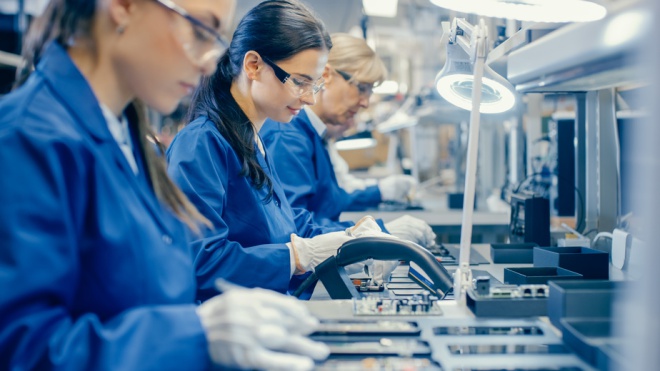
多品種少量生産、多頻度小口輸送で複雑化する製造現場
大量生産時代には、工場の生産ラインをフル稼働させながら特定の商品を集中的に生産するスタイルが一般的だった。その際、工場の物理環境は稼働中に変化しない(=静的である)という前提があり、その前提のもとに資材調達量や在庫量の最適化や生産能力の分配が行われ、その状況はある程度機能していた。
しかし、多品種少量生産の時代に移り変わりつつある中で、工場の物理環境は流動的なものとなった。
具体的には、製品のラインアップが多くなったため生産ラインの切り替えを行う回数がかなり増加し、複数の工業機械のセッティングを行うための“段取り”という作業が増えた。この段取り時間が稼働率の低下を引き起こし、生産の円滑化を妨げている。また、多頻度小口輸送やジャストインタイム配送、24時間配送が増えたことで、出荷時のオペレーションが複雑化している。
「プラントデータアナリティクス」が課題解決の突破口に?
これらの課題は、もはや現場の人間の勘や経験によって対処できる範囲を超えており、アルゴリズムを活用した効率的な生産スケジューリングに対する需要が日々増している。ただし、いくら需要があってもすぐ課題が解決できるわけではない。これまでの生産管理ツールは過去の実績や各種のデータをベースにしたシミュレーションに基づく部分が多かったが、物理環境の流動化によって考慮すべき変数・状況が増え、満足のいく解を出すのが難しくなっていた。
実績やデータをベースにしたシミュレーションでは、分析に用いる数理モデルがあらかじめ決まっている。各種生産要素の数量を入力し、連立方程式を解く要領(解析的手法)で最適解を導き出す。しかし、変数が増加したために計算量が増大し、実務時間内で解析的に処理できないケースや、そもそも解析的処理が行えないケースが発生することもある。
従来の生産管理ツールは、数式に組み込む変数の数を減らすことでこの問題を回避してきたが、根本的な解決には至らなかった。そうした中、データを活用して帰納的に近似解を導く「アルゴリズムデザイン」の研究が進んだことで、工場の生産現場へのデータアナリティクスの導入が急速に進んでいる。
生産管理で活用される「近似解を導くアルゴリズム」
産業が近代化するにつれ、企業の生産管理には科学的な方法が導入されるようになった。それにより、実社会で企業が直面する経営課題や生産管理上の課題は、数字および複数の方程式の集まりである数理モデルとして表現できるようになった。実際、企業は機械の力を活用して数理モデルを解き、生産管理の最適化を試みてきた。このモデルを解くための手順が、いわゆる「アルゴリズム」である。しかし、消費者行動が変化し、生産体制も高度化し、生産管理課題の数理モデルはどんどん複雑になってきている。これまでのアルゴリズムで数理モデルを完全に解くことが難しくなり、完全解の代わりである近似解が重視されるようになってきた。そこで、「近似解を求めるアルゴリズム」の需要が増してきた。
こうした中で近年、アルゴリズムの導き出す近似解が意思決定に使える程度に正確になり、データアナリティクスが実務者にとってアルゴリズムが魅力的な選択肢になった。工場内の機械の配置・稼働のタイミングやリードタイム、歩留まりの詳細など、物理環境の細部まで計算式に含みながらも、実用的な答えを出すことができるようになったのだ。
「遺伝的アルゴリズム」とは?
こうしたアルゴリズムの具体例の1つが「遺伝的アルゴリズム」である。遺伝的アルゴリズムは、生物の進化過程を模倣したアルゴリズムであり、短時間で精度の高い組み合わせパターンを導く。
遺伝的アルゴリズムは、大量に用意した組み合わせパターンを「選別」したり、「掛け合わせ」たりして適切な組み合わせパターンを作り出す。
コメの品種改良のイメージにたとえると分かりやすいだろう。我々がいま食べているコメは、沢山ある品種の中から強く生産量の多い品種同士を交配させることで誕生している。それと同様のプロセスを遺伝的アルゴリズムは計算機上で行い、より理想的な組み合わせパターンの生成を行う。
自然界のシステムでは、環境に適応した生物が繁殖と世代交代を経て生き残る。遺伝的アルゴリズムでは、決められた制約条件(環境)を最も理想的な形で満たす組み合わせパターン(生物)が望ましい近似解として生き残る。
【次ページ】遺伝的アルゴリズムを活用したデータ分析とは?
関連コンテンツ
PR
PR
PR