- 会員限定
- 2017/09/20 掲載
GEのモデル工場、Brilliant Factoryを現地で見てきた
前編はこちら(この記事は後編です)
GEのモデル工場、Brilliant Factoryを見てきた
GEのモデル工場である日野工場では、ITとIoTの導入により生産性向上に取り組んでいる。建屋は地下1階、地上5階。地下1階にCTディテクタ(検出センサー)、1階にCTガントリ(大きな輪の架台)、2階に超音波診断装置用プローブの各製造ラインがあり、3階が生産管理とコールセンター、4階が営業・サービス・技術部、5階が社員食堂になっている。公開されたのは、地上1階の一部のゾーンだ。製造の大まかな流れは、まず地下1階で製造されたCTディテクタや、外部サプライヤーから調達した各種部品が、機種ごとの「キットカート」としてサブラインで準備される。これは、毎回これらの部品を倉庫から取ると効率が悪いためだ。
次にメインラインにて、作業者がカートから部品を取り出し、CTガントリを組み立てていく。ここで標準化が行われており、作業順とキットカートから取る部品順がリンクしているため、作業者は悩まずに作業を進められる。
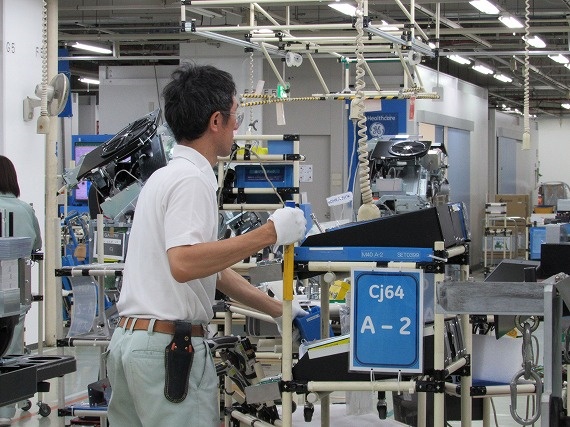
また、作業自体は1時間内に終わるように設定されている。このため、キットカートの開始と終了のタイミングをRFIDで検出することで、どのくらい進捗しているのかをリアルタイムで把握できる。
これらのデータはExcelで自動処理され、カラー別に進捗状況がディスプレイに表示される。黄色や赤色の場合は進捗に遅れがあるため、トラブルをエスカレーションし、作業の改善が行われるという流れだ。データはすべて記録されており、あとから継続的な改善も可能だ。
製造工程の改善の取り組みを、医療現場の改善にフィードバック
各部品の不良などの品質についてもシステムに記録され、どの工程で、どんな不良が、どの部品番号で起きたのかといった詳細データを吸い上げ、ダッシュボードに表示される。これは、前出の産業用ソフトウェア・プラットフォーム(Predix)のアプリケーション「Manufacturing Hub」だ。工程管理については、専用の「BOX PLOT」と呼ばれるツールで示される。
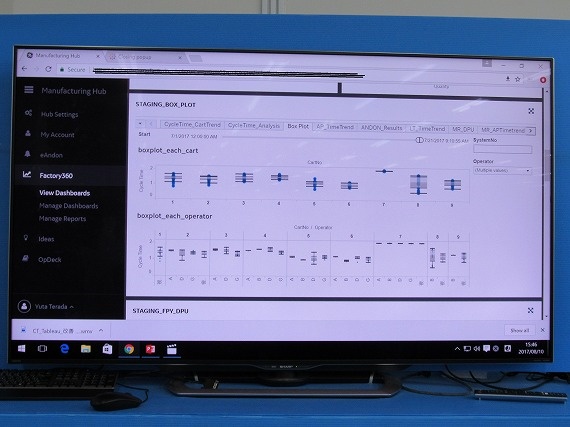
標準の作業時間に対して、各キットカートでの作業時間が計測され、プロセスごとに一覧表示される。そのバラつきを調べることでボトルネックを解消し、全体を最適化するための知見が得られる。
さらに作業時間のバラつき具合は、作業者ごとに分析することも可能だ。作業者のノウハウを聞いて作業手順を組み替えたり、調整したりする改善活動につなげていく。
このようにして、同工場では1日に2台というハイペースで高度な医療機器であるCTが製造され、全世界の病院に出荷されている。特に日野工場における製造工程のバラつき分析・管理に関しては、医療関係者からも「医療現場の改善活動に応用できる」との反響が寄せられているという。
医療現場におけるCT検査プロセスでも、検査技師によってどのようなバラつきがあるのかを調べたり、改善活動の機会につなげることに活用できるからだ。
【次ページ】工場レイアウトの最適化にもデータを活用
関連コンテンツ
PR
PR
PR