- 会員限定
- 2021/03/08 掲載
なぜ安川電機が「植物工場」? 億単位の損失を出したときに社長がかけた言葉とは
連載:イノベーションの「リアル」
-
|タグをもっとみる
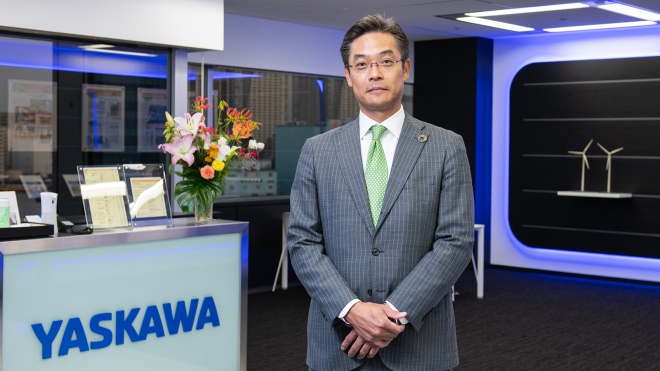
安川電機からスピンアウト、植物工場システムを開発
(アクト・コンサルティング 野間 彰 氏)──まず、FAMSの事業について教えてください。森田氏:我々は安川電機のモーションコントロールやロボット、エネルギー変換などの技術を活用して、独自コンセプトに基づいた自動ソリューションを展開しています。具体的には種まきから、間引き、移植、収穫までを自動化した完全人工光型の野菜生産システムの開発と販売を行っています。もう1つの事業では、食品製造分野を中心に、包装、パレタイザーなどの各種ロボットを利用した自動化を手掛けています。
──植物工場にロボットを適用し、自動化を図ろうとしたのは、いつからでしょうか?
森田氏:実は2012年から始まっています。当時、私は安川電機に所属しており、モーションコントロール事業部のエンジニアでした。2015年に安川電機は100周年を迎えることから、そこに向けて新規事業の種を探すためにマーケティング部が作られました。そこに2012年から配属され、1次産業にアプローチしていくことになり、翌年から植物工場の自動化システムのプロジェクトが立ち上がったという経緯です。
安川電機は、ロボット、サーボ、インバーターなど産業機械の分野では世間に広く認知されていますが、1次産業の方々には知られていなかったため、最初はご挨拶しても「どこの電気屋さんですか?」という反応からのスタートとなり、大変苦労しました。
──森田さんの安川電機での役職や立場は、2012年当時は1つのプロジェクトを任されたチーム長であったということですか?
森田氏:そうです。それまでは安川電機の課長という立場でチームを引っ張っていました。2018年に現在のFAMSが設立され、上司だったマーケティング部の部長が初代社長になりました。そのとき私は取締役として片道切符で転籍しまして、2019年から社長に就任しました。
野菜を「コマ」で管理、ロボットによる自動生産システム
──新規事業で混沌としていた状況から、新しいものをつかんだり発見したりといった、そういう「感動」はありましたか?森田氏:FAMSはメーカーですから、やはり「三現主義」(現場・現物・現実の3つの「現」を重視すること)がべースになっています。現在の完全人工光型の野菜生産システムを立ち上げる際も、まずは一般的な野菜システムを購入し、実際にいろいろ栽培したり、システムを調査したりしてアイデアを発見しました。
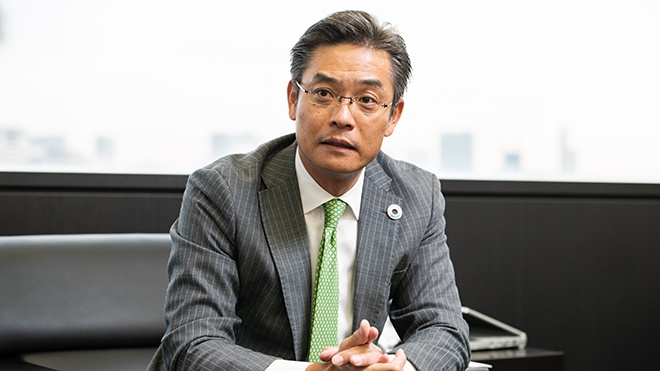
代表取締役社長
森田 卓寿氏
植物工場の一般的な野菜の育て方では、1つの大きな発砲スチロールに5株なり10株なりの野菜を穴の中に入れ、成長にしたがって穴の間隔が広いものに植え替えていきます。当初、我々はそのシステムを導入して、どうやったらこれを「自動化」できるかを考えました。
システムは高さ4m×長さ10m~20mほどあるので、作業者が高所で作業し、成長した野菜を植え替える必要がありました。安川電機にはロボットやモーションコントロールの技術と経験がありますから、「コマ」という発想が出て、これが大きな特徴になりました。このアイデアを思いついたときは「よしこれだ!」 と思いましたね。
──そのアイデアは、従来のシステムとどのように違うのでしょうか?
森田氏:我々のシステムは、野菜を1株1株、先ほどのコマで管理していきます。ロボットで、このコマを把持して株を各段に移しながら、野菜の成長とともに間隔を広げていくのです。そのため種まきから収穫まで、基本的に人による作業が不要という業界初のシステムになり、特許も取得しています。
このコマにも、いろいろな形状があり、工夫が凝らされています。穴径や大きさによって、野菜の根の張り具合や成長が違ってくるのです。システム自体はまだ完成ではないと思っていますし、やっているうちに課題も必ず出てきますので、PDCAを回しながら改良を加えているところです。
社内公募で選ばれたエンジニアと関連会社プロパーの協力で難問を解決
──これは、どうやって思いついたのですか。突然ピンと閃いたのでしょうか?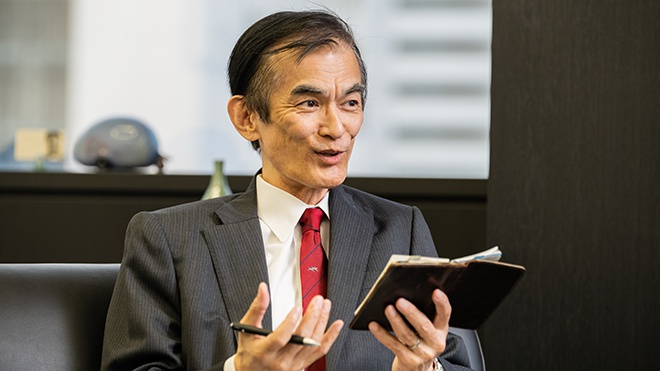
取締役 経営コンサルタント
野間 彰氏
森田氏:思いつくためのポイントは2つありまして、1つは野菜の成長につれて間隔を広げなければならない点です。もう1つは自動化する上で、ロボットでつかむシーンが必ず発生する点です。我々がロボットメーカーだからこそ、こういった発想ができたのかもしれません。
──なるほど。このアイデアは最初に誰が思いついたのですか?
森田氏:安川電機の社内公募制で集ったエンジニアです。プロジェクトを立ち上げた当初は人が集まるかどうか不安もありましたが、3名の定員で希望者が20名ほど集まり、大変ありがたかったですね。そこで人事と相談しながら、「植物工場をやりたい」という信念を持つ開発リーダーを選びました。安川電機が持つロボットやモーション技術を集約すれば、必ず何か生まれるという強い思いがあったんですね。
人材面では多くの関係者に尽力いただきました。現在、本社は新潟にありますが、施設は半導体やフロッピーディスクドライブ(FDD)製造を行っていた関連会社ワイ・イー・データのものでした。実はそこを2018年にFAMS本社・工場にして、安川電機から関係者11名を異動させ、それ以外の約50名弱は、ワイ・イー・データに在籍していたプロパーの人々に協力してもらいました。
我々だけでは多くの難問をクリアできなかったでしょう。材料特性などの技術知見を持った専門家が、レールの形状や熱収縮の課題などに一緒に向き合ってくれたからこそ、できあがりました。そういう意味で本当にうれしい話で、この野菜生産システムの中には「FAMSの魂」が宿っていると感じています。
【次ページ】億単位の損失、そのとき社長から掛けられた一言
関連コンテンツ
関連コンテンツ
PR
PR
PR