- 会員限定
- 2022/09/26 掲載
東レの「発明王」に聞く、なぜ炭素繊維で2,100億円超の売上を作れたのか?
連載:イノベーションの「リアル」
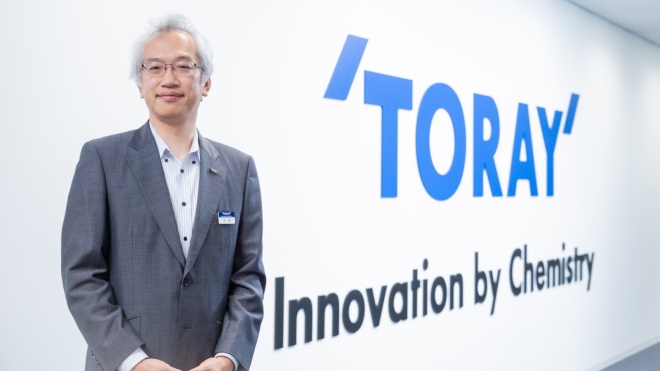
リサーチフェロー
複合材料研究所 研究主幹
本間 雅登氏
軽くて強い炭素繊維複合材の実用化に立ちはだかる課題
(アクト・コンサルティング 野間 彰氏)──基本的な話で恐縮ですが、そもそも炭素繊維複合材料とはどういうものでしょうか?本間 雅登氏(以下、本間氏):複合材料は強化材と母材を加えたもので、たとえば鉄筋コンクリートは砂・砕石・鉄とセメントを混ぜたものです。複合材が高性能化して「先端複合材料」となり、炭素繊維とエポキシ接着剤などの樹脂を混ぜた炭素繊維強化樹脂、いわゆる「CFRP」(Carbon Fiber Reinforced Plastic)が登場しました。
炭素繊維は比重が小さく、一方でガラス繊維などの強化用繊維よりも単位重量あたりの強度・弾性率が圧倒的に大きく、耐熱性・耐薬品性・耐腐食性も優れています。モノを軽くしたいなら炭素繊維を使うのが工業材料の定石です。ただし炭素繊維は単体では構造体として使えないので、樹脂(プラスチック)と合わせて成型します。
基材として「プリプレグ」(PP)がキーワードになります。これは約7μmの炭素繊維を引き揃えたシートに樹脂に浸み込ませたものです。炭素繊維は繊維方向に強度を持つため、色々な方向に積層するラミネート構造にして等方向性の強度を持つCFRPになります。
成型は、圧力窯で蒸し焼きにする「オートクレーブ」が一般的です。あとから樹脂を一気に入れる「レジントランスファーモールディング」(RTM)という方法もあり、自動車部品などに使われます。用途用法で方法を考える必要がありますが、オートクレーブを使ったPPが最も特性が出ます。ただし窯で樹脂を固めるため10時間ほどかかります。射出成型も可能ですが、その場合は炭素繊維を細切れにして樹脂と一緒に型に流し込みます。その結果、力学特性が出にくいのが弱点です。
ジェット機の一次構造材にも CFRPの歩みと市場価値の高まり
──炭素繊維の歴史と、具体的な用途について教えてください。本間氏:東レは約50年前の1971年に炭素繊維の商業生産を始めたのですが、最初の10年は底を這(は)うような状況でした。しかし当時の経営判断で、炭素繊維のポテンシャルを信じて開発を続けてきました。
軽くて強い特性から、最初はゴルフクラブや釣り竿などのスポーツ用品から実用化が始まりました。徐々に大きな用途、たとえばボーイングの一次構造材に認定され、ボーイング787では機体構造がオールコンポジット(複合材)になりました。今、コロナ禍で航空機産業は試練を受けていますが、2025年には回復し、再拡大するでしょう。
当初、CFRPは量産化が難しかったのですが、東レは先ほどのRTM技術を極める大型国家プロジェクトに参画しました。従来160分かかっていた生産時間が10分で作れるようになります。このようにして炭素繊維の市場価値を高めるとともに、その成形加工にも大胆なメスを入れCFRPの用途を開拓してきました。
──本間さんはCFRPについて本当に色々な研究をされてきたのですね。
本間氏:最終製品になる道筋には、いくつもの要素技術が求められます。どれか1つでも欠けるとモノにならないのです。材料メーカーはスペックにこだわりますが、その材料がどのような使われ方をして、どのように機能するのか、最後製品の観点から考えていなければなりません。そこにかかわる全ての技術が研究対象となります。たとえ採用されなくても、要素技術としてどこかで役立つこともある、こういう発想を大事にしています。
量産化技術でノートPCに採用されるも、新たな試練
──PC筐体へのCFRP適用は、その後の開発に影響を与えたと聞きました。本間氏:当時から、ノートPCは薄く軽量な製品が求められていました。ノートPCの筐体には、一般的な汎用樹脂から、マグネシウムの合金、CFRPなどのハイエンド素材が使われていました。PC筐体には電子部品の保護と内部のスペース確保が重要となるため、素材のデザインは悩みどころでした。
東レの場合は、1997年にIBM ThinkPadの筐体にCFRP射出成形材料を採用していただきました。薄さと軽量を求めつつ、採用の決め手はEMI対策(ノイズ対策)で、筐体に電波シールド性を持たせるというものでした。炭素繊維は電気を通すので、繊維が長いと回路を構成できます。そこで繊維が長い長繊維ペレット「TLP(Toray Long carbon fiber reinforced Pellet)」を開発し、事業を拡大しました。
ところが2002年になって、キラーアプリのマグネシウム合金の射出成形加工品が出てきたのです。相手が金属になった途端に、TLPは性能面で劣勢になり、IBMさんから最後通牒を突きつけられたのですが、1回だけチャンスをもらいました。「マグネシウムと同じ重さと剛性を維持して、ある薄さになれば、TLPを採用し続ける」という営業情報でした。その開発時間はわずか3カ月。それでも新材料を開発しました。しかし結果的に不採用でしたね(笑)。
──お客さまの言う通りの材料を作ったのに、なぜ不採用になったのですか?
本間氏:メーカーとしては、製品に「トータルの薄さ」を求めていたのですが、設計を繰り返すうちにだんだんと厚くなった。そうなると、マグネシウム合金の方が薄くできて有利になったのです。それ以降、ターゲットスペックをそのまま受け入れるのではなく、顧客はどのような価値を求めているのかちゃんと理解しようと決意しました。これは今も実践しています。
ただ、失敗しても諦めないことが大事です。射出成形で最高のものを開発しても勝てないなら、もう発想を一から変えよう、ということになりました。
【次ページ】負けたからこそ完成できた「ハイブリッド加工法」で起死回生へ
関連コンテンツ
PR
PR
PR