- 会員限定
- 2022/07/19 掲載
ヒントはアイススケート? 三機工業「世界最速」搬送仕分け装置の開発秘話
連載:イノベーションの「リアル」
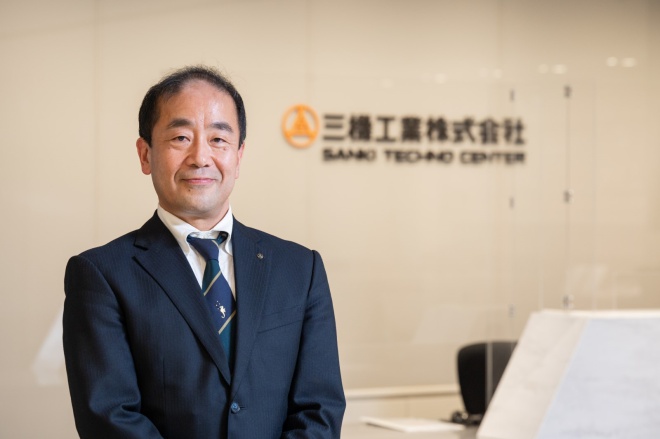
R&Dセンター 機械システム開発部長
菱沼 信也氏
新規国際空港の案件を奪取して、BHSを復活させよ
(アクト・コンサルティング 野間 彰氏)──世界最速のコンベア開発、きっかけは何だったのですか?菱沼 信也氏(以下、菱沼氏):空港物流では、「BHS」(Baggage Handling System)と「CHS」(Cargo Handling System)の両方やっています。ただ一時期BHSが落ち込み、2006年開港の新規国際空港整備計画の中で、物流システムを受注するために社内プロジェクトが発足しました。そこで私がリーダーになり、「クロスベルト式自動仕分け装置」を開発したという経緯があります。
──BHSのシェア挽回を目指したわけですね。
菱沼氏:はい。当時の事業部長が若い頃にBHSを担当しており、思い入れもあったようです。それで新規国際空港の案件を絶対に取ろうと。弊社は当時、建築・設備、環境がメインで、機械は目立っていなかったので、国際空港で受注するのは大きな挑戦でした。しかし受注が成功して、社内でも一目置かれるようになり、機械システム事業部も変わりました。
入札に勝つためにヨーロッパまで視察、コンセプトを練り直す
──新規国際空港の受注は事業部門にとっても重要なプロジェクトだったのですね。競合に勝つためにどうしたのですか?菱沼氏:コンセプト作りのために、当時、仕分け装置技術で先行していたヨーロッパまで視察に行き、現地空港の方と話をさせてもらいました。そこで、今使っているシステムの「欠点」を聞き、欠点を克服して現状システムを凌駕する新しいコンセプトを、「低振動、低騒音、省スペース対応型高速仕分け」と定めました。
高速に伴う騒音と振動、信頼性の担保、メンテナンス性が課題に
──当時の問題点は、どのようなところにあったのですか?菱沼氏:クロスベルト式は、コンベヤ台車を水平方向に旋回させ、各間口に搬送物を仕分ける機構ですが、空港内を高速で走行するため、出発ロビーのお客さまへの振動・騒音が問題になります。また300~400mの距離を走行するため、カーブ部の曲率半径の関係で、広大な設置スペースが必要となる等、レイアウト性に問題がありました。信頼面も高速走行時の車輪寿命を含め、メンテナンスも大変。またコンベヤ台車のリンク部が走行時間に応じて伸びてくるので、詰めなければなりません。あと電装品を交換するのも時間がかかるなど課題が山積みでした。
──これを全部解決するのは大変ですね。
菱沼氏:そうですね。たとえば振動・騒音については、ヨーロッパのメーカはカーブ部を走行するときに内輪と外輪の軌跡が同心円にならず、車輪の首振りが起き振動、騒音の原因となっていたので、我々は同心円にするアイデアで振動・騒音を軽減することができました。またレールの据付精度が悪いと走行時に連結リンクにストレスが掛かり軋み音が発生するので、従来は現場でのレール据付時に高い精度が求められました。我々はカートの連結リンクに捩れ機構を搭載することで、逆に軋んでも吸収できる仕組みにして、音も振動も小さくしたのです。
──こうした解決方法を何個も見つけてきたわけですね。
菱沼氏:ええ。考えて、実験しての繰り返しでした。振動・騒音の解決は大変でしたが、これらが解決できれば、機械に加わるストレスも小さくなるので破損もなくなります。他にも、さまざまな工夫を凝らして、実運用に耐え得るものになりました。
──こうしてできたのが「CBⅠ」。競争相手に勝って見事納入できたわけですが、その時はどうでしたか?
菱沼氏:納入したシステムが動くのを、チェックインカウンター裏で見ていました。それはもう、感動しました。社内の見方も変わりました。ちょうど会社として、「総合エンジニアリング」の方針が出て、事業部を超えて顧客に価値を提供するという時でした。他の事業部の顧客を紹介してもらい、納入業界の幅が広がりました。
──その後の「CBⅡ」、最新の「CBⅢ」と開発を進められた?
菱沼氏:CBⅠで基礎技術を確立し、CBⅡで標準化とコストダウンを図りました。そこで競争相手がコンベヤの高速化で対抗してきたのです。当社120m/min、競争相手は160m/minでした。そこで、当社比で倍の240m/minを目標にCBⅢを開発。世界最高速を達成しました。
アイススケートがヒント? 世界最速を達成するための努力と苦労
──速度が倍ですか。一体どんな工夫をされたのですか?【次ページ】大きな課題を分解して考えると、1つずつ解決できる可能性も
関連コンテンツ
PR
PR
PR