- 会員限定
- 2017/02/02 掲載
IHI 村野 幸哉 執行役員に聞くIoT戦略、グループ共通プラットフォームの狙いと成果は
後編はこちら(この記事は前編です)
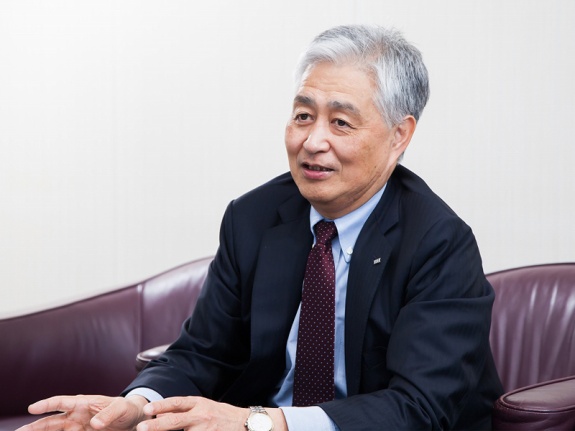
高度情報マネジメント統括本部長 執行役員
村野 幸哉 氏
2週間でプロトタイプを作って見せないと機を逸する
村野氏:中期経営計画「グループ経営方針2013」では、成長に向けたグループ共通機能の強化をテーマに、「各事業体の製品・サービスとICTをつなぐ」、「既存事業間および既存事業と周辺事業をつなぐ」、そして「グローバル市場とIHIグループをつなぐ」という、3つの「つなぐ」に取り組みました。
ICTに関しては、2013年4月に「高度情報マネジメント統括本部」を設立し、共通プラットフォームの整備と、IHIグループのリソースの集中を両輪で加速させてきました。2013年からの3年間は、センサーから集めたデータを分析して、お客さまへの価値提供を行う基盤整備と、併せてモデル事業体と具体的な価値創造を模索した期間と位置づけることができます。その取り組みが少しずつ花開き、2016年度からは、IHIの取り組みをより多くのお客さまへ展開させていただく段階に入ったと考えています。
──「グループ経営方針 2016」の進捗状況などについてお聞かせください。
村野氏:「グループ経営方針2013」での3年間の成果や反省を踏まえ、2016年4月からは、グループ共通プラットフォームを、よりお客さまへの価値提供につなげていく取り組みを行っています。具体的には、「製品・サービスの高度化」と「ものづくりの高度化」という2つの取り組みを進めており、共通プラットフォームの整備から「お客さまへの価値提供」に軸が移ったということです。
──その中で高度情報マネジメント統括本部が果たす役割とは何でしょうか?
村野氏:高度情報マネジメント統括本部は、2013年4月に約30名のチームとして発足し、2016年3月時点で約50名に拡大しました。2016年4月からは、これまで組織として並立して活動してきた情報システム部と合併し、新たに「高度情報マネジメント統括本部」として再編、今は約120名のチームで動いています。
もともと、高度情報マネジメント統括本部は、技術開発本部や各事業部門で制御系の技術開発を行っていた人材を集めており、IoTに近い領域を担当していました。そこに情報システム部が加わり、現場の制御装置やセンサーから収集したデータをクラウドに蓄積、分析を行い、さらにお客さまの価値を創り出すプロセスがワンストップで行えるようになり、重複する業務の非効率さが解消されました。
──今、主にIoT関連のプロジェクトを担うのは、統括本部の中のどの組織になるのですか?
村野氏:主に高度情報マネジメント統括本部の中のIoTプロジェクト部が担当します。IoTプロジェクト部は、プロジェクトマネジメントを統括する「プロジェクトグループ」や、ものづくりの高度化を担当する「スマートファクトリーグループ」、データ分析を担う「情報科学技術グループ」、そしてIHIグループ共通IoTプラットフォームを担当する「プラットフォームグループ」に分かれており、業務と人を集約し、「製品・サービスの高度化」「ものづくりの高度化」「情報分析力」の強化と加速に取り組んでいるところです。
──統合組織の強みはどこにありますか?
村野氏:鍵はスピードです。今はユーザーのビジネスのスピードが早くなり、たとえば、当社の工場で「こういうデータが見たい」という話になると、2週間くらいでプロトタイプを作って見せないと機を逸してしまいます。そうしたスピード向上を主眼に組織改革を行いました。
15年以上、紙で記録・保管してきた整備データが「宝の山」に
──グループ共通のIoTプラットフォームとして取り組む「ILIPS(IHI group Lifecycle Partner System)」とはどのようなものですか?村野氏:ILIPSは、製品の稼働データを収集し分析するためのリモートモニタリングプラットフォームです。具体的には、航空エンジンや発電用ガスタービン、汎用ボイラ、自動倉庫、真空浸炭炉などの製品・サービスや、プラント建設現場や自社工場などの多岐にわたる場面で活用しています。また、「CSIGS(Control System of IHI group)」と呼ぶ制御共通プラットフォームも整備しています。これは、通信機能を持つIHI製のデータ収集装置と制御装置を統合させた装置で、これを機械に設置することで、取得したデータを、M2Mやインターネットにより容易にILIPSへ通信することが可能になりました。
プラットフォーム化の経緯としては、IHIグループには26の異なる事業体がありますが、これらが個々にデータを収集し分析する基盤を構築することは効率的ではありません。また、分析技術もビジネス領域が違っても転用可能な技術が多くあり、そうであればデータ収集基盤と分析手法をプラットフォームとして共通化したほうが効率が高まると考えました。
──貴社の位置付けるM2Mとは、インターネットではなく専用線を使っているということでしょうか?
村野氏:M2Mは基本的に3G回線を用いてデータを送信しています。もちろん、プラント系など大量のデータを扱うものはインターネットを使うものもありますが、M2Mの場合、インターネットに比べセキュリティに優れている利点があります。
──モノごとにデータの型などが異なる中で、プラットフォームの共通化は難しかったのではないでしょうか。
村野氏:扱うデータ量は違いますし、必要なデータの収集周期も異なります。かつ、スピードも求められる中で、最適なデータ収集のあり方は実際に運用してみないとわからないというのが正直なところでした。そこで自前のインフラにこだわることなく、運用しながら柔軟にチューニングしていくことができるクラウドをインフラに採用しました。弊社としては新しい試みといえます。
──機械側に設置するCSIGSは、新規に開発したのでしょうか?
村野氏:CSIGSは、これまで当社がガスタービンなどで培ってきた、制御装置に関する約20年のソフトウェア資産を活用し、ハードウェアについてはコスト面を勘案しながら、産業機械に使いやすいよう新規で開発しました。
とはいえ、お客さまにとっては、制御装置に関する新たな投資をお願いすることになるので、我々は「制御装置の入れ替え」ではなく、「新しい付加価値の付与」である点をご理解いただくよう働きかけています。
──こうしたプラットフォーム整備の背景には、これまで「データはあるが活用できない」というような課題があったのでしょうか。
村野氏:リモートモニタリングの仕組みは、ガスタービン発電装置やパーキング装置などの保守管理の領域で、15年くらい前から仕組みを整備、活用してきた事例がありますが、グループ全体でセンサーから自動的にデータを収集するIoTの取り組みが始まったのは、数年前からでした。
一方、この取り組みを通じて初めて気づいたのですが、社内のサービス部門の人間が、お客さまの現場に入って、膨大な保守データを紙に記録し、そうした記録が現場部門に保存されていたのです。大体どこのサービス部門でもこうしたデータを記録していたのですが、紙に記録されたデータの多くはファイルに綴じられて、キャビネットに保管されたままで、うまく活用できていませんでした。
そこに着目しない手はないだろうということで、我々は紙のデータをうまく活用する仕組みを考えました。
センサーデータの取り組みはここ数年くらいですが、紙の整備記録は15年くらいの蓄積があります。どの機械で、いつ、どういうトラブルがあったか、そのトラブルに対して、どういう整備をして問題を解決したかという記録は、大変重要な資産となっています。
【次ページ】発電プラントに約300点のセンサーを取り付けたらどうなったか
関連コンテンツ
関連コンテンツ
PR
PR
PR