- 会員限定
- 2016/06/03 掲載
MBD(モデルベース開発)はもはや必然、ホンダ 大津啓司常務が語るその理由
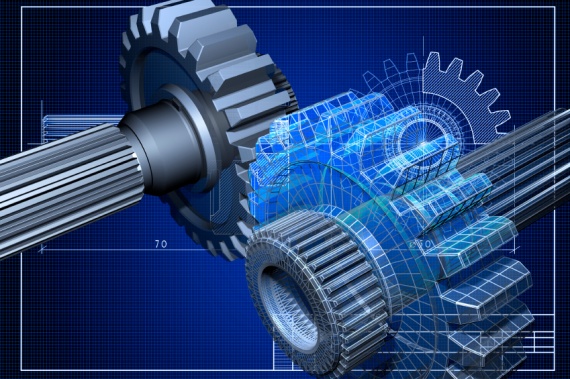
自動車業界の厳しい現実と、ホンダの技術への対応
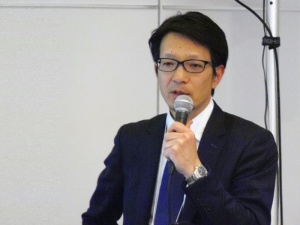
四輪R&Dセンター
常務執行役員
技術戦略担当
大津 啓司 氏
「なぜホンダが多様な製品を開発しているのか。それは人に役立つことを突き詰めているからだ。創業者の本田宗一郎は『ホンダ研究所は人を研究する場所だ』と言っていた。つまり、人が欲しいものを研究し、それを実現するとき、初めて技術が必要になる。そこで我々は、創業者の意思を脈々と引き継ぎ、このような多くの製品の開発を行っている」
「年間で約4%ずつCO2を削減しないと、このレギュレーションにミートできない。IEA(国際エネルギー機関)は、遅くとも2050年までには自動車の電動化が必要だという。ここで特に注目したいのは、内燃機関を搭載した車両も2040年までは増加するということだ(ハイブリッドを含む)。つまりコンベンショナルなエンジンを搭載したクルマの燃費を向上しながら、CO2規制に対応していかなければならない。内燃機関と電動化の両輪による進化が求められている」
そのような状況で、ホンダは優れた安全性能と環境性能をベースに、FUNを表現することを掲げ、顧客の感動を目指す考えだ。
「地球環境と走る喜びを高次元で両立させる“EARTH DREAM TECHNOLOGY”のコンセプトによって、多くのパワートレイン(動力伝達系)を開発してきた。NA(自然吸気)からターボエンジン、ハイブリッド、最新トランスミッションでは10速のATまで対応している。エンジンについては、熱効率を上げるために自然吸気と過給のエンジンをつなげて進化をさせていく。これが1つ目の内燃機関のキーテクノロジーだ」
なぜホンダはMBDを導入したのか? そのメリットと現状の課題
もう1つ、同社のキーテクノロジーである電動化技術は、これまでハイブリッドを中心に普及してきた。「しかし今後はゼロエミッションに向けて、PHEV(プラグインハイブリッド)や“ZEV”(ゼロエミッションビークル)にシフトする方針だ。PHEVはゼロエミッションまでの橋渡しとなる技術として重視している」
このような進化によって、10年前と比べて技術も多様化し、ホンダのみならず、他の自動車メーカーも開発負荷が大幅に増えているのが実情だ。
「たとえば、ガソリンエンジンの骨格の刷新サイクルをみても、5骨格を8年間で開発していたものが、いまや5骨格を2年間で開発するほど日程が縮まった。制御系の開発サイクルも複雑化し、10倍の制御負荷になった。自動運転技術を組み込むためには膨大な制御系とデータを実装しなければならない。このような開発の負荷に対応する解決策が、MBDということになる」
昔は各クルマに対して、それぞれ専用エンジンを開発していたが、いまはクルマとエンジンのプロジェクトに分けて開発するようになった。対応できるトルクバンドのエンジンを複数ぶん用意し、それを多種の車体に乗せるというアプローチだ。ホンダは、ハイブリッドの拡大によって複雑化する開発を見越し、すでに2008年からMBDを導入したそうだ。
「これまでの開発の実態は、量産開発のほうにウェイトが置かれすぎていた。そこで開発リソースをうまく配分し、先行開発するフロントローディングの手法が求められている。これによって、ある程度の失敗も許されるようになる。失敗は一見すると無駄に見えるようだが、人材開発面でも長い目でみれば悪いことではない」
MBDでは、初期工数はかかるものの、あとで一気に精度を上げられる。論理的に仕様を決め、グレーな部分に開発を集中することで、初期図面精度を向上させ、開発期間の短縮と競争力の強化が図れるのだという。
従来のように、設計後の検証段階から手戻りするような非効率なプロセスを踏まない。各階層でモデルを駆使し、設計段階からシミュレーションを行いながら、迅速にフィードバックを行い、しっかりした設計仕様をフィックスできる点が最大のメリットだ。
「MBDによって、設計初期のモデルから完成車の性能を予測し、手戻り工数の抑制が可能だ。さらに実機の確認で同定されたモデルを、次のロットでも再利用し、予測精度を上げられる」
とはいえMBDを適用しても、まだ課題は残されてるという。
「CAEによるシミュレーション技術は進化してきたため、初期の図面精度は上がっている。しかし知見の少ない新技術では、背反性能の項目を洗い出しきれない。そのため実際には手戻りが起きて、ハード系の完成度も遅れてしまう。そうなると、今度は制御系でハード系を補うことになり、開発の負荷が増えてしまう」
【次ページ】MBDは競争領域だが共創領域でもある
関連コンテンツ
PR
PR
PR