- 会員限定
- 2017/03/29 掲載
今さら聞けない3Dプリンターの基本と仕組み、どんな事例があり、どこがシェアトップか
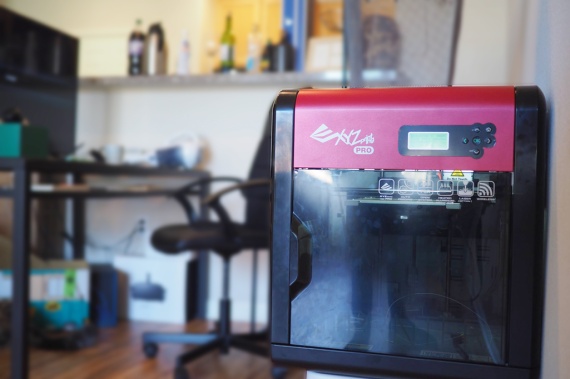
3Dプリンターブームが起きたワケ
当時の3Dプリンターは完全に産業用の世界で何千万円クラス。大手企業が製品開発時の試作作成のプロセスで使用するという位置づけだった。その数年後には(個人向けにも)3Dプリンターブームがくるわけだが、当時は想像もつかなかった。
この間に何が起きたのだろうか? まずは、3Dプリント技術が登場した経緯を振り返ってみよう。
3Dプリント技術、発明の歴史
3Dプリント技術が研究開発された背景には、1970年代から始まる「Rapid Prototyping」の流れがある。技術革新と普及、個々人の嗜好の多様化、マーケットの変化といったさまざまな要因のもと、製品開発において試作製作・評価のプロセスの見直しが求められるようになった。
すばやく(rapid)試作(prototyping)し、テスト・評価期間を経て、レビューを元に再度、試作に戻る。こうしたプロセスを繰り返すことで、より精度の高い製品を開発できるのではないかと模索が始まり、1980年代には立体をメカニカルに造形する技術についての研究が日米で同時多発的に起こる。
当時設計の世界も3D CAD化されつつあり、そのまま立体造形ができれば試作(プロトタイプ)のプロセスを短縮できる。光硬化性樹脂などの新しい素材技術の登場もあった。
1980年、光造形法の特許を小玉秀男氏(当時、名古屋市工業研究所に所属)が世界ではじめて出願した。光造形法とは、CADデータから作成された断面データをもとにレーザーを液状の光硬化樹脂の表面に照射することで造形を行うというもの。現在に至る代表的な3Dプリント技術の方式だ。翌1981年には日米で論文を発表している。ただ、当時は産業界からの反応は芳しくなく、実用化には至らなかった。審査請求を行うことなく、特許権は発生しなかった。
また、小玉氏とほぼ同時期に、3MのAlan J. Herbert氏が1982年に論文を発表。3Mでは事業化は難しいと判断し、ここでもそれ以上研究開発を進めることはなかった。
大阪でも丸谷洋二氏(当時、大阪府立工業研究所)が光造形法による立体造形の研究を始めていた。丸谷氏は1984年に特許を出願。さらに、その3ヶ月後にChuck Hull氏が同じく光造形法の実用化に関する特許を米国で出願した(日本での出願は1985年のこと)。
世界ではじめて実用化された製品としては、Hull氏が設立した3D Systemsの「SLA-1」となる。3D Systemsの事業化を受け日本の企業も動き出し、1988年に三菱商事が丸谷氏と共同開発した「SOUP」を販売開始する。
このように光造形法という技術の開発・実用化の動きは日米で相前後して起きている。それだけ時代のニーズだったということなのだろう。なお、光造形法の研究開発に関する歴史はWeb上にある北口秀美氏による文献が詳しい。
RPシステムから「3Dプリンター」へ
光造形は高精細で、滑らかな表面の造形物を作成することが可能だ。しかし、材料となる素材が高価であり、空調設備や洗浄装置などの設備が必要という大掛かりなシステムになる。Rapid Prototyping System(RPシステム)として売り出されていくが、ランニングコストが高いため、実際に導入できたのは大手企業がほとんどだった。一方、ほぼ同時期に光造形法以外の技法も出てくる。先行技術の実用化が特許で守られているのだから当たり前といえば当たり前だが、「積層して立体の形にする」ことを原理として、その積層を実現するさまざまな技術が生まれた。
1986年に米国テキサス大学の教授を中心とし粉末焼結積層造形法(SLS : Selective Laser Sintering)に関するプロジェクトが発足。翌1987年にはSLS方式の3Dプリンターの製造・販売を目的としてDTM社が設立されている(実際に製造が開始されたのは1992年)。
また、1989年にスコット・クランプ氏が熱溶解積層法(FDM : Fused Deposition Modeling)を特許出願。クランプ氏が創業したStratasysはFDMによる3Dプリンターを製造・販売している。
こうして1990年初頭には主流となる3Dプリント技術の方式がそろったわけだが、現在、これらの技術に関する基本特許が切れたことで、さまざまな企業が参入し、市場に数多くの製品が投入されてきているという状態なのだ。
3Dプリント技術に関する主な特許 | ||||
特許の概要 | 発明者 | 出願人 | 補足 | 満了年 |
Apparatus for production of three-dimensional objects by stereolithography [US 4575330 A] | Charles W. Hull | Uvp, Inc. | ステレオリソグラフィーによる3次元物体の製造装置 | 2004年 |
Apparatus and method for creating three-dimensional objects [US 5121329 A] | S. Scott Crump | Stratasys, Inc. | FDM方式(熱溶解積層法の1つ)の重要特許 | 2009年 |
Apparatus for producing parts by selective sintering[US 5597589 A] | Carl R. Deckard | Board Of Regents, The University Of Texas System | SLS方式(粉末焼結方式の1つ)の重要特許 | 2014年 |
もちろん、重要な基本部分に関する技術が使えるようになったというだけであって、それ以外の、たとえばより品質を上げるための工夫であったり、既存の製品には複数の技術が使われているが、そうした技術の特許はまた別になる。そのため、先行の製品と同レベルのものがすぐさま出てくるというわけではない。
従来から使われている「RPシステム」に対し、「3Dプリンター」という言葉が使われたことも大きい。紙に印刷する2次元のプリンターに対して立体を造形する3Dプリンター。特にFDMの特許切れにより、デスクトップに据え置く形の家庭用の3Dプリンターが登場した際、この言葉はイメージがつかみやすかった。そこがブレークするポイントだったといえる。
オープンソースの3Dプリンター開発プロジェクト「RepRap」とは
2006年には、英国の研究者が中心となって、オープンソースの3Dプリンター開発プロジェクト「RepRap」を立ち上げた。基板やパーツの設計図、制御用のソフトウェア、作成マニュアルなどすべての情報を公開し、それを使って誰もが自由に作れるというもの。2007年に試作機「Darwin」、2009年に「Mendel」、2010年に「Huxley」を公開している。積層方式としては、システム構築がシンプルなFDM方式。FDMがStratasysの持つ商標のため、RepRapプリンターはFFF(Fused Filament Fabrication)という呼称を用いる。
RepRapプロジェクトが目指した3Dプリンターのポイントは3つ。
- 3Dプリンターが自分のパーツ(すべてではないが)を印刷することができる
- 自身でプリントできない部品は低コストで入手できる
- オープンソースで、デザインを無料でインターネットから利用できる
RepRapプロジェクトは各国各地に広がっており(日本にもRepRap Community Japanがある)、さまざまな人たちが協力し改良や拡張を行って、現在では、大型機として「MendelMax」、小型機として「Wallace」など、さまざまなバリエーションが登場している。
2009年にFDMの特許が切れたというタイミングもあり、以降、RepRapプロジェクトからの派生で、多くの家庭用3Dプリンターが生まれている。
FDMは光造形に比べて微細性や滑らかさには欠けるが、ある程度強度のある造形が可能。試作品や簡易型の造形には十分だ。当時Makerムーブメントの隆盛し始めた時期であり、相性は抜群だった。こうして、2010年前後にさまざまな個人向け3Dプリンターの登場で、一大ブームが起こる。
まさにRepRapプロジェクトがそうだが、誰もが使える、改変できる、拡張できる、それによってより発展していく。オープンソースという文化が、これまで特許で縛られてきた3Dプリント技術を個人の手にまで届けたと言える。
しかし、こうしたオープンソースが牽引した3Dプリンター市場は成長するにつれビジネスとしての難しさにも直面した。ここでは詳しくは触れないが、RepRapプロジェクトから派生したMakerBot Industries(2009年設立)は、当初のオープンソースというポリシーを後に変更。現在はStratasysに買収されている。
3Dプリント技術の仕様・規格をまとめ
ここで、3Dプリント技術について、仕様・規格的な部分をまとめておこう。一般的に3Dプリントと言われるが、国際的な工業規格ASTMでは「Additive Manufacturing(付加製造)」と定義されている。「材料を付着することにより物体を3次元形状の数値表現から作成するプロセス。多くの場合、層の上に層を積むことによって実現され、除去的な製造方法と対照的なもの(ASTM F2792-12a)」ということになる。
図で示すのは特許庁による技術動向調査報告書のものだが、3Dプリント技術(本稿では、この用語をそのまま用いる)を、造形に用いる材料について、あるいは3Dモデリング(3D CADや3D CG)で扱うデータ方式などの3Dデータ処理、3Dモデルデータから立体に造形する技術、装置の機構や制御方式など、さまざまな複合技術からなる、ととらえている。
また、次の表はASTMが分類する3Dプリントの製造方法、いわゆる「どう積層するか」の部分だ。主に7つに分類される。
このように、3Dプリント技術にはさまざまな方式がある。何を作るか、何のためにそれを使うのか、どういう使い方をするのか(短期利用か長期利用か、など)、どれくらいのコストをかけられるのか、などにより、当然、適した製造方法(材料)は異なる。
積層方法の違いはあれど、基本的な生成プロセスのフローを単純化してみると次のようになる。
以下、補足しておくと、出力用3Dデータ形式としてはSTL形式が現在標準的に用いられている。これはChuck Hull氏の発明したもの(1983年)で、3つの頂点座標と法線ベクトルにより定義される三角形ポリゴンを持つオブジェクトからなるデータフォーマットだ。表面の面、メッシュに関する情報しか持たないシンプルなもの。
しかし、3Dプリント技術が対象とする造形物がより機能的になれば、データも複雑化する。データフォーマット側がそうしたデータを持つことができないとなれば、当然、各メーカーごと、機種ごとに対処することになるが、それではデータの汎用性が低くなってしまう。そこで、データフォーマットを見直すため、STLの代替となるAMF形式がASTMにより制定され、2013年に標準化した。徐々に3Dソフト側の対応も進んでいく。
またサポート材およびラフ材は、形状をデータ通りに造形するために用いる。不安定な3Dの形状では固まるまでの間に、歪みが生じてしまう。それを防ぐために、形状を支えためのものだ。
なお、造形の精度には、出力用3DデータかGコードに変換するスライサーソフトの性能も大きく関係する。3Dプリンターのによってはスライサーの設定をあらかじめ機種や材料に合わせてあり、変えられないようになっている場合もあるが、上位機種のほとんどでは機種や材料、造形物の特性などに応じ、調整が可能なスライサーソフトを用いることができる。
世界/国内の3Dプリンター市場動向は?
ここまで仕組みについて解説してきたが、3Dプリンターを利用する人や企業は拡大しているのだろうか? 矢野経済研究所による世界市場調査(2016年9月~11月調査)によれば、2015年の世界の3Dプリンター出荷台数は前年比72.7%増の19万台となったという。60万円未満の個人向けローエンド3Dプリンターと60万円以上の産業用ハイエンド3Dプリンターの二極化が進んでおり、出荷台数を牽引するのはローエンド装置。簡易かつ迅速に試作を行うための導入が進むほかに、教育機関での導入が増加基調にあるそうだ。また同調査によれば、世界の3Dプリンター出荷台数は、2013年から2019年までの年平均成長率は77.0%で、2019年における出荷台数(メーカー出荷数量ベース)は215万台になると予測した。
国内はどうだろうか。IDC Japanが2016年7月に発表した調査結果によれば、国内の本体出荷台数は前年比20.2%の大幅減となり、一時のブームは落ち着いた格好となった。ただし、企業利用は着実に増加しており、総売上額では4.4%増。また、2015年から2020年までの総売上額年間平均成長率は15.3%と予測しており、今後も拡大するとの見立てだ。
【次ページ】3Dプリンター製品のシェアトップは?
関連コンテンツ
PR
PR
PR