- 会員限定
- 2022/06/02 掲載
八子知礼氏・福本勲氏らが激論、「DX未着手」が約6割……製造業DXが進まない根因とは
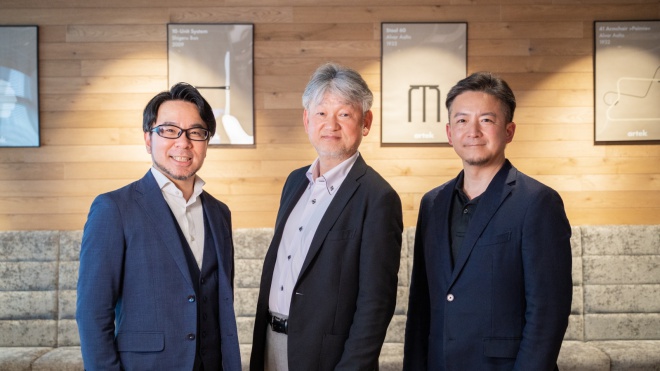
なぜ製造業にDXが必要なのか? 「4つの理由」とは
今や業種・業界を問わず、あらゆる企業が取り組んでいるのがDXだ。ただし、DXに取り組む理由は業界によって異なる。それでは、製造業がDXに取り組むべき理由は何だろうか。東芝 デジタルイノベーションテクノロジーセンター チーフエバンジェリストの福本勲氏は「製造現場のノウハウ継承が困難になったこと」「ものづくりの競争力の維持」「製品変化への対応」「業務のリモート化ニーズの拡大」の4つのポイントを挙げる。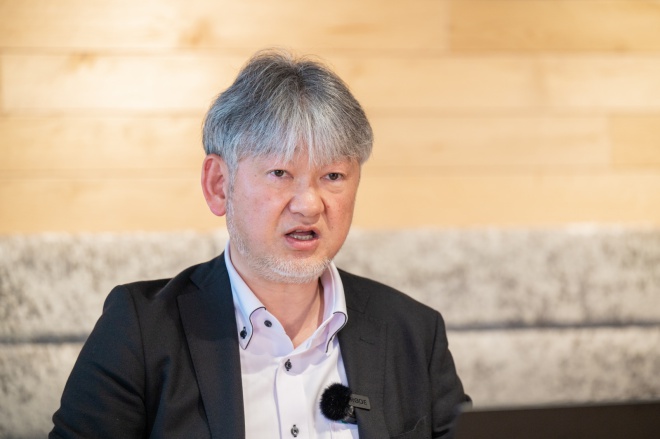
チーフエバンジェリスト
福本 勲 氏
「日本の製造業は、これまで匠のノウハウを人から人に継承してきました。しかし、生産年齢人口が減少する中、培ったノウハウをすべて人に継承することは難しくなってきています。そのため、今後は可能なかぎりデジタルに継承できるノウハウはデジタルに継承していく必要があり、そのためにも製造業はDXに取り組むべきなのです」(福本氏)
2つ目は競争力の維持だ。福本氏は、「日本企業の生産現場では、数十年前の機械がいまだに動いていることも珍しくありません。一方、海外はゼロベースから最新設備を導入している工場がたくさんあります。そうした状況下でも、ものづくりの競争力を維持することが求められており、その鍵となるのがDXというわけです」と語る。
さらに最近は、製品が複雑化しソフトウェア制御の範囲が増えていることから、従来のように製造現場のノウハウだけで品質を高めることが難しくなってきた。また、顧客に製品を納入した後にもソフトウェアのアップデートなどを通じて、製品を使う顧客のニーズに常に対応していくことまでを考えたものづくりが求められている。このような環境変化に対応するためのDXは欠かせない。
そして4つ目がリモート対応だ。コロナ禍の影響により、リモートでの作業支援やメンテナンスの仕組み作りが求められている。
日本のDXが遅れている「3つの理由」
それでは現在、日本の製造業のDXはどれくらい進んでいるのだろうか。福本氏は、DXの取り組み状況を調査したIPAの「DX白書2021」から、日米の比較データを示しながら現状について次のように話す。「データを見ると、DXに取り組んでいる企業は日本が約56%、米国が約80%と約24%の差があります。このデータを業種ごとに見ると、特に製造業での差が顕著で、日本は約20%(一部門の取り組みと合わせて45.3%)、米国は約44%(一部門の取り組みと合わせて74.2%)となっています。それだけ製造業のDXが遅れているのです」(福本氏)
なぜ、日本のDXは遅れているのだろうか。福本氏は、日本のDXが遅れている原因として次の3つを挙げ、それぞれを解決すことが重要だと強調する。
- (1)IT化やデジタル化が目的になってしまう
- (2)IT人材が自社にいないため、ITベンダーに依存する傾向がある
- (3)取り組みが既存ビジネスの延長線上での効率化に偏重する傾向がある
一方、製造業のDXが進まない原因を「魔のデッドロック」という表現で別の視点から指摘するのが、INDUSTRIAL-X 代表取締役の八子知礼氏だ。
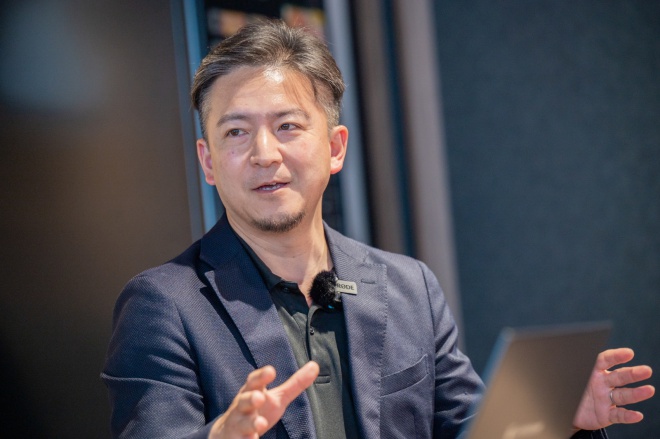
代表取締役
八子 知礼 氏
「DXを進めようとしても、古い設備がボトルネックになります。そこで設備を入れ替えようとすると『その機械でないとダメ』という現場の人が出てきます。つまり今度は人がボトルネックになります。また、作業などの属人化解消のためにデジタルツールを活用しようとすると、ツール利用に求められるリテラシーやスキルがボトルネックになります。このように、『物理システム』『ヒト』『デジタル』の3要素が相互にボトルネックとなり、がんじがらめになってしまう状況が『魔のデッドロック』です」(八子氏)
したがって、人のマインドセットを変え、業務を自動化する際には、その業務に携わっていた人たちの教育・リスキリングを充実させて、心理的な安全性を担保するなどの取り組みが重要になると八子氏は指摘する。
【次ページ】製造業の脱炭素、「排出量の把握」が超重要なワケ
関連コンテンツ
関連コンテンツ
PR
PR
PR