悩めるIT部門に告ぐ。品質と生産性向上のカギは、現場の「腹落ち感」だ
- ありがとうございます!
- いいね!した記事一覧をみる
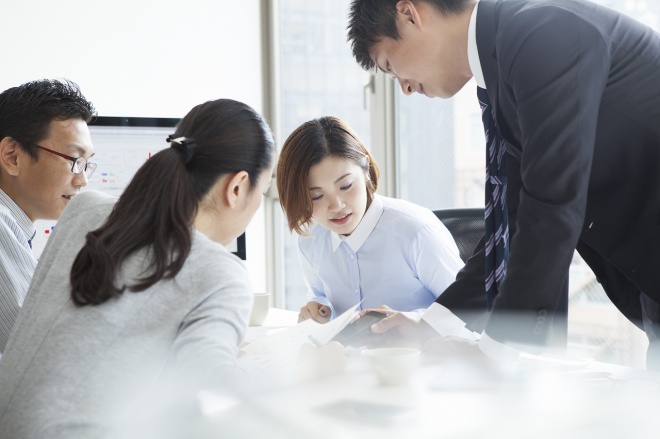
当事者意識を育てる「腹落ち感」とは?
すべての業務に共通することだが、いくらトップダウンの施策があっても、現場が自分事に落とし込まなければ、やがて形骸化してしまう。品質・生産性の改善活動に欠かせない要素は、現場が目的をしっかりと理解し、「腹落ち感」を持って取り組める体制づくり、いわば「ボトムアップの仕掛け」である。これにより現場のマインドやモチベーションも上がり、現場で適切な判断と決定ができる。結果的に企業の組織力や継続力も向上するのだ。
では、この「ボトムアップの仕掛け」とは、具体的にどのようなものだろうか。端的にいうと「個人の底力を上げ、パフォーマンスの最大化を目指す仕組み」のことだ。チームメンバーの意見から課題や問題点を共有し、解決策を納得するまで全員で検討して、それを日常業務で実践していく。この活動サイクルを継続していくことが大事なのである。
実際に品質や生産性向上を実現した企業は、どのような過程を経ているのだろうか。ここからは事例をもとに成功のポイントを探っていこう。
・障害件数が1/3、開発損失額が1/5に。中央集権型から分散型への大転換
・大手製造業事例、階層別の課題解決アプローチで品質改善
・腹落ち感を持ちつつ、日常業務の“一部”になることが重要
障害件数が1/3、開発損失額が1/5に。中央集権型から分散型への大転換
かつてTISも、自社の品質・生産性に課題を抱えていたという。もちろん同社は品質マネジメントシステム(以下、QMS:Quality Management System)を導入していた。しかし、それは中央集権型のトップダウン施策であり、本部が決めた細かい規定の開発標準を現場に遵守させるものだった。TISで企業組織のPMO支援サービスを行っている小櫃靖夫氏は「我々のQMSはもともと中央集権型で、細かな規定を遵守する現場とその管理部門において負担が大きく、現場業務との乖離も少なからず発生していました。開発や保守・運用で一定量の障害や不採算案件も存在していたのです。そこで2015年から事業部・部門のボトムアップを併用した分散型の新たなQMSを導入しました。現場の裁量を拡大することで、創意工夫を最大限に生かせるようにしたのです」と当時を振り返る。
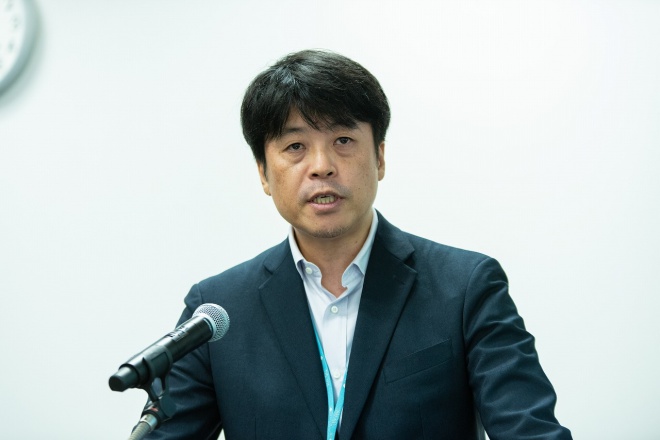
小櫃(おびつ)靖夫氏
TISでは、このようなQMSの見直しと並行し、保守改善の推進部門を新設したり、現場支援の強化や、チーム力の向上にも努めた。つまり前出のボトムアップの仕掛けや、腹落ち感を重視した体制にシフトしたのだ。これにより障害や不採算案件を大幅に削減することに成功したという。
「新たなQMSを導入することで、全社の開発損失額を5分の1まで減らし、開発損失率も1%以下にすることができました(2017年実績)。また保守運用における障害件数も、3年間で3分の1まで漸減できたのです」(小櫃氏)
この成功を受けて、TISは自社の品質改善で蓄積されたノウハウを他社にもビジネス展開し、品質活動を支援しているところだ。以下、某大手製造業における代表的な成功事例を見ていこう。
大手製造業事例、階層別の課題解決アプローチで品質改善
これは某大手製造業の支援事例だ。同社では、従来の製品がデジタル化され、事業転換が必要になったことに加えて、拡大するITニーズに対する開発力の拡充が急務となっていた。「すでに同社は、ICT関連の品質活動や標準化に向けた取り組みを進めていました。しかし現場に品質活動が定着せず、赤字プロジェクトも減らないまま、システム障害も頻繁に繰り返されていたのです。その状況を打開すべく、本質的な課題解決が可能な品質活動と継続的な仕組みを求めていました」(小櫃氏)
依頼を受けたTISは、自社で培かってきたノウハウから「プロジェクト実行支援」「診断/アセスメント」「組織支援」「PM(Project Management)教育支援」という4種のメニューを用意し、診断/アセスメントと組織支援を提供した。
まず診断/アセスメントによって、チーム力と保守・運用業務を診断し、その結果から課題を可視化して品質・生産性を高める改善活動を展開した。さらに、それらを土台として組織支援として標準化の策定を行ったという。
小櫃氏は「ここでは階層別に課題を解決するアプローチを採用することで、品質管理を継続的に向上できる組織と意識改革を目指しました」と説明する。
この階層とは、デジタルビジネスを支える「風土、マインド、モチベーション」「日々の仕事のやり方」「プロジェクトマネジメント(PM)」「ITエンジニアリング」という4つのレイヤーを指す。それらに対して本事例では「チーム力向上」「保守・運用改善」「標準策定」を適用した形だ。
腹落ち感を持ちつつ、日常業務の“一部”になることが重要
小櫃氏は、本事例で適用した個別支援サービスについて、より詳しく解説した。初期診断の主な目的は、チーム力を高め、現場が主体となって課題を解決できる組織を目指すこと、さらに保守業務における品質を向上し、現場で見えない課題の可視化と改善活動の定着を図ることだ。TISの診断/アセスメントには「チーム力向上」「システム保守」「システム運用」の3種がある。「現状分析」「深層分析」「差異分析」という統計的手法を用いて課題を分析・可視化して改善活動につなげるのだ。
「我々の支援により、"これまで現場に改善活動が定着しなかった理由や課題が明確になり、経営層にも具体的な理由を説明して、協力を仰げるようになった"という感想をいただけました」(小櫃氏)
その次にTISは大手製造業の標準策定に着手した。その主な目的は、事業部の特性に合わせ、開発プロセスや成果物の基準を策定し、今後のデジタルビジネス拡大に伴うシステムリスクを低減することにあった。
TISでは、自社のQMSやPM支援のノウハウを基に、ICT開発に必要な標準策定のサービスをオーダーメードで対応している。ユーザーの経験やリテラシーに合わせ、現状把握、標準策定、改善活動の展開・支援までをサポートするものだ。具体的な標準策定の流れは以下のとおりだ。
まず現状把握のために、現行の開発標準とTISの開発標準を比べてフィット&ギャップを行い、洗い出された課題やリスクを解消することで、期待できる効果を明らかにして標準化方針を決定。そのうえで各プロセスを定義し、プロセスごとにガイドラインやフォーマットを策定していった。
「この際に具体的なイメージや対応方針を変更しながら、どんな改善ができるのかを現場と一緒に考えながら進めていきました。現場で継続利用が可能なものを作成することが大きなポイントです」(小櫃氏)
この標準化策定により「要件定義や外部設計において、何のために、どこまで標準化を進めるべきなのか、その判断軸が明確になり、自分たちの言葉で自らが使う標準を高めていける実感がつかめた」というユーザーの声をもらえた。これは、まさに現場が「腹落ち感」を持って、改善策を継続利用してくれたリアクションであった。
最後に小櫃氏は「現場が腹落ち感や当事者意識・責任感を持ち、日常業務と一体となった活動を継続していくことが肝要です。個人の底力を上げ、パフォーマンスを最大化する。つまり現場主体で、臨機応変に連動して動ける"有機的な組織"に変える必要があるのです。我々は、新たな企業価値を生み出し、みなさまのビジネスに貢献できる人材や体制を作り上げる仕組みを、今後も提供していきます」と強調した。