- 会員限定
- 2021/05/07 掲載
新たなDX人材像「ファクトリーサイエンティスト」、中小製造業の“等身大のDX”担う
中小企業で「IoT」導入が進まない理由
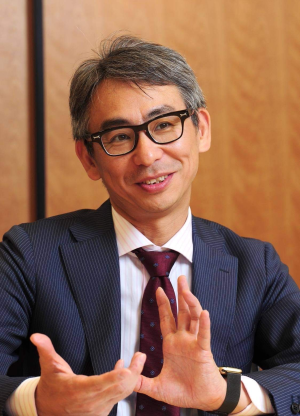
ローランドベルガー シニアアドバイザー
長島 聡 氏
「DXによって現場で働く人々がデジタルの目と手をしっかり身につけ、従来の困りごとを解決できるようになれば、省人化で捻出できた余剰時間を新たな価値の創出や稼ぐ力のために活用できるようになります」(長島氏)
捻出できた時間を使って、これまで出会ったことのない多様な企業と協創できれば、新たな収益案件が生まれる可能性もある。またヒヤリハットや予知保全、労働環境の改善、夜勤や休日出勤をなくすリモート監視、過酷環境での負担軽減、最近ではコロナ禍における感染防止の観点でも、DXで可能性が広がる。
とはいえ、中小企業のIoT導入が順風満帆に進んでいるかというと、現状ではそうでもないようだ。もちろん「IoTに取り組むべき」という感覚は誰もが持っているが、人材面や資金面の課題もあるからだ。長島氏は現場の声を次のように代弁する。
「現場では人的リソースが足りず、IoTまで手が回らなかったり、IoT技術に興味があっても社内で仕様を書ける人材がいなかったりします。ベンダーが提案に来ても価格や機能の妥当性が分からず、費用対効果も見極められないので、発注ができないのです」(長島氏)
「ファクトリーサイエンティスト協会」をなぜ設立したのか
こうした問題意識の中で、2020年4月、「ファクトリーサイエンティスト協会」が設立された。同協会は、モノ作りで注目されている由紀ホールディングスの代表 大坪 正人氏と、慶応義塾大学 SFCの田中 浩也教授、登壇者の長島氏などが発起人となり、現場起点のIoT人材育成や資格認定を目的とした一般社団法人である。長島氏は、協会を設立した意図を次のように説明する。「現場の課題抽出から計画立案、課題解決、報告までの一連の活動を一気通貫で担えるIoT人材の育成を目指しています。まずは小さな課題を“手触りのあるIoT”で解決し、徐々に大きな課題に挑戦していく人材を育てたいと考えています」(長島氏)
協会の名に冠されている 「ファクトリーサイエンティスト」(FS)とは、工場現場を科学し、会社全体を巻き込み、工場の稼ぐ力を向上させる人材のことだ。求められるのは「データエンジニアリング能力」「データサイエンス力」「データマネジメント力」の3つのスキルである。
「データエンジニアリング能力」は、現場の課題をデータで明らかにするために、どんなセンサーを工場のどこに設置し、どれくらいの頻度でデータを取得したら良いのかをエンジニアリングするスキルだ。
「データサイエンス力」は、現場からクラウドにアップされたデータを組み合わせて、工場の生産性や経営に意味があるデータに加工・分析するスキルを意味する。
そして「データマネジメント力」は、現場の課題をもとに、企画立案から予算取り、チームや現場を巻き込んで意思疎通を図ってシステムを実装し、最終目標まで持っていける管理スキルである。
「ファクトリーサイエンティストはこのようなスキルを身につけ、工場の作業者と工場長、社長をつなぎます。サイエンスの力を使ってデータというファクトに意味を持たせながら、工場の生産性を上げる役割を担うのです。我々は、2030年までに全国で4万人のファクトリーサイエンティストが活躍する社会を目指しています」(長島氏)
なお、「4万人」という目標値の根拠は、国内企業の事業所が20万ほど存在していることに由来している。5事業所に1人程度の割合でファクトリーサイエンティストがいる状態にしたいという思いからだ、と長島氏は語る。
FSを育成する5日間のプログラムとは
現在ファクトリーサイエンティスト協会では、人材育成のために全5日間のプログラムを用意し、受講者に対して実践と対話を繰り返しながら自律的な学びのサイクルを構築している。1日目はローカル側のシステム基礎で、センサーやマイコンなどを学ぶ。センサーそのものについてはもちろん、センサーの機械への取り付け方、治具を3Dプリンターで作成する方法も含まれている。2日目はサーバ側システムの基礎だ。クラウドにMicrosoft Azureを使い、データのアップロードと加工、データベース構築等を行う。3日目はデータ加工とビジュアライゼーションを学び、4日目は現場や経営者を動かすための「見える化」や「見せる化」の追求に取り組む。
そして仕上げの5日目は、協会理事などを社長に見立てたプレゼンテーションで、費用対効果やネクストステップの発表まで行う。
「ファクトリーサイエンティストとして最終的な"ありたい姿"を明確に描き、現場にIoTを実装していきます。ただし、いきなり大きな案件に取り組むのではなく、最初の一歩として手短にやり切れることから始め、成功体験を積み重ねることを目標にしています」(長島氏)
そのため、まず現状の見える化と課題の特定から始めるという。工場には、設備・工具、材料・半製品・製品があり、職人・作業者がいるが、まず設備や工具においては、それらの性能を引き出した状態で使って、稼働率を高め、より多くの製品を世に送り出せるようにする。
材料・半製品・製品の観点では、買った材料を、可能なかぎりすぐに使って製品化して販売する。つまりサプライチェーンの観点からも、モノが滞留する状況を作らないという視点が重要だ。人については「IoTを助手」として考え、仕事の守備範囲を広げ、楽しくて単価が高く取れる仕事に注目する。
「2019年夏は、こうした内容で合宿を行い、受講者が深夜まで作業に没頭しました。2020年のコロナ禍では、完全オンラインに移行しました。マイコンやセンサーなどが入った認定デバイスキットを事前配布し、インストラクション動画なども交えて復習できるように工夫しました。2021年5月には春講座を始め、夏にはe-learningも開設する予定です」(長島氏)
オンラインとはいえ、講師のほかにTA(Teaching Assistant)と呼ばれる技術アドバイザーを4-5名準備し、Slackなどのツールも活用することで、IoTを自社工場に実装する際に困ったことも相談できる体制を実現した。その結果、リアルにも劣らない受講者同士の交流や協力体制を構築でき、会社同士の協創の話に発展する良い循環も生まれているそうだ。
【次ページ】受講生が手掛けたIoTシステム3事例、FSが備えるべき7つの資質
人材管理・育成・HRMのおすすめコンテンツ
PR
PR
PR